Anil Lokesh Gadi discloses AI-support framework to optimize engine performance in real time
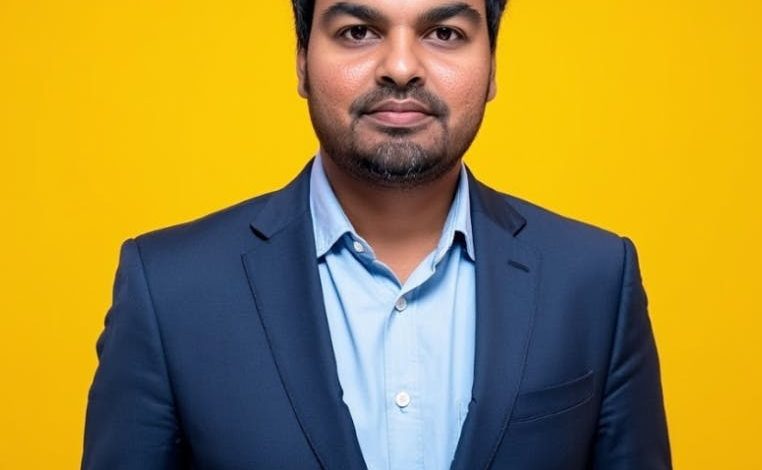
Ani Lokesh Gadi, a technology manager and scientist, has been an important contributor to the more efficient and smart contribution of engine tracking systems. Through his research, he has come up with AI-support framework capable of preventively
Gadi's research has led to a scalable and practical solution that uses internet sensors to allow continuous monitoring and malfunctions. In addition, his framework can be integrated with machine learning models capable of analyzing the real -time sophisticated data sets. This integration allows for a predictive analysis that increases the overall efficiency of the engine while reducing unplanned downtime.
Need to improve engine performance tracking
In today's industrial landscape, which continues to be more digitized during the day, the restrictions and deficiencies of the usual engine diagnostics have become more perceptible. These traditional systems are strongly dependent on rudimentary primary care, manual inspection and threshold warning systems. These methods often do not provide real -time intelligence for timely intervention. As a result, the impairment of performance, increased downtime, unexpected malfunctions and expanded maintenance costs may go unnoticed.
The engines have also become more sophisticated with the advent of electronic control units (ECUs) and interdependent subsystems. Without access to advanced analysis and deep telemetry, it is extremely difficult to identify the factors leading to performance problems for human operators. Contributions are extremely high in industrial sectors, where safety and continuity of work are the main priorities, such as production, electricity generation and transport.
Through his research, Anil Lokesh Gadi has responded to an ever-increasing need for change by presenting a dynamic, ai-controlled alternative. With a preventive approach, his real -time diagnostic framework is constantly scanning anomalies and predicts failures before it affects performance.
Understanding the framework
The flexible architecture that combines intelligent data pipelines, IoT-based sensors and strong machine learning algorithms form a nucleus of Gad
- Acquisition of data and pre -processing: At the beginning of the framework, IoT sensors are used in the key components of the engine, such as fuel nozzles, crankshaft, exhaust units and cooling systems. These sensors perform the telemetry collection function at various vital parameters such as speed, vibration, temperature and pressure. Due to the incompetent nature of such data, specific pre -treatment routines are also added to these systems. This routine involves handling missing values, filtering anomalies, ensuring temporal synchronization and normalization of diverse data.
- Hybrid deployment: Architecture also achieves a balance between the calculated depth and real -time response, supporting the introduction both in the cloud (for the aggregated analytics) and at the edge (on the edge or near the engine). EDGE COMPUTING provides low latency malfunctions that are important for time -critical operations. On the other hand, cloud -based systems provide the total knowledge of the total park, historical trend analysis and long -term performance forecast. This hybrid control model makes the solution cost -effective, scalable and applicable in all types of industries.
- Intelligent Classification Classification: The framework offered by GAD uses nerve networks and machine learning models, such as supporting sectors (SVM) and random forest engine classification based on databases. These models have been trained to detect both the resulting anomalies and the known malfunction patterns through pattern recognition. Respect of new data inputs allows these models to provide high adaptability and accuracy. This makes them a suitable broad important condition and engine architectures.
Advantages in the whole industry
Gadi argues that its framework has a far -reaching effect and broad applicability in many different industries, where the operative vertebrae strongly depends on the engines and mechanical systems.
- Transport and automotive industry: Real -time diagnostics can help car manufacturers and logistics park operators improve fuel efficiency, reduce roadside distributions and extend engine life.
- Railroad and aviation: Aviation and rail operations require improved malfunctioning systems as safety is extremely critical for these sectors. The GAD framework can be customized for complex systems and larger engines by providing reliability.
- Energy and utilities: Gas turbines and diesel generators are in two areas in the electricity generation sector, where this system can be extremely useful in reducing emissions, ensuring electrical supply and monitoring engine critical health parameters.
- Industrial equipment and production: This framework can be used to monitor the engines used in heavy duty processing systems, generators and CNN machines at production plants. Predicting potential malfunctions will allow plant managers to design repairs during the planned under -timing, which prevents production tests and minimizes losses.
Conclusion
The Ail-powered diagnostic framework, presented by Anil Lokesh Gadi's potential for motor performance is important. He is confident that it will pave the way to manage the health of the machine to create a smarter and more responsive way.
“The designed architecture not only can diagnose engine failure, but it is also scalable and customizable for different types of industrial engines and work environment,” Gadi concludes. “This system is an important step in integrating intelligent diagnostics into modern industrial systems.”